Ph.D. associate professor SŁAWOMIR PIETROWICZ Eng.,WUST PROF.
PH.D. PRZEMYSŁAW BŁASIAK Eng., PH.D. JÓZEF RAK Eng.
DEPARTMENT OF THERMODYNAMICS AND RENEWABLE ENERGY SOURCES,
WROCŁAW UNIVERSITY OF SCIENCE AND TECHNOLOGY
Ph.D. associate professor SŁAWOMIR PIETROWICZ Eng.,WUST PROF.
PH.D. PRZEMYSŁAW BŁASIAK Eng., PH.D. JÓZEF RAK Eng.
DEPARTMENT OF THERMODYNAMICS AND RENEWABLE ENERGY SOURCES,
WROCŁAW UNIVERSITY OF SCIENCE AND TECHNOLOGY
Use of high computing power for design analysis and optimisation of large-scale industrial mixers with consideration of thermal-fluid processes
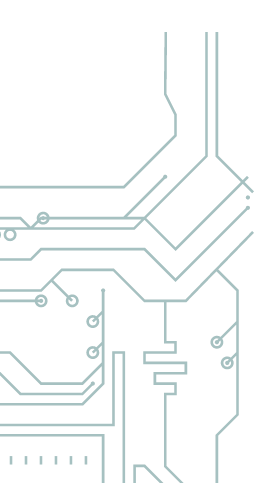
PROJECT OBJECTIVE
Problem
The project concerns the development of methodology for carrying out advanced CFD (Computational Fluid Dynamics) type numerical calculations using high computational power dedicated to industrial mixers. This is crucial for the design and optimisation of mixers with large volumes, i.e. above 6 m3, where the reduction of mixing time and efficiency results in large savings related to energy inputs.
Project objective
Development of mathematical models of mixing processes and their implementation in commercial and open source numerical software. During the project, the models were validated and ultimately used during the design of the optimised mixers. Design elements directly involved in the mixing process, such as mixing/dispersing discs, anchors and elements supporting the process, were optimised. In addition to the flow processes, both thermal processes resulting from the friction of the mixed products and the heat input from the heating/cooling systems installed in the unit were implemented in the models. The final result of the optimisation process is a mixer characterised by shorter mixing times and a more effective, efficient cooling and heating system.
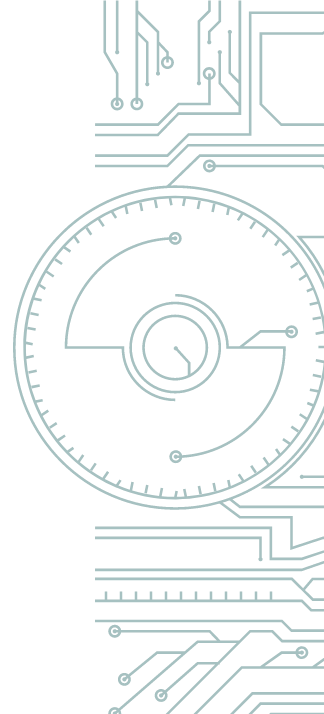
CEL PROJEKTU
Problem
The project concerns the development of methodology for carrying out advanced CFD (Computational Fluid Dynamics) type numerical calculations using high computational power dedicated to industrial mixers. This is crucial for the design and optimisation of mixers with large volumes, i.e. above 6 m3, where the reduction of mixing time and efficiency results in large savings related to energy inputs.
Cel projektu
Development of mathematical models of mixing processes and their implementation in commercial and open source numerical software. During the project, the models were validated and ultimately used during the design of the optimised mixers. Design elements directly involved in the mixing process, such as mixing/dispersing discs, anchors and elements supporting the process, were optimised. In addition to the flow processes, both thermal processes resulting from the friction of the mixed products and the heat input from the heating/cooling systems installed in the unit were implemented in the models. The final result of the optimisation process is a mixer characterised by shorter mixing times and a more effective, efficient cooling and heating system.
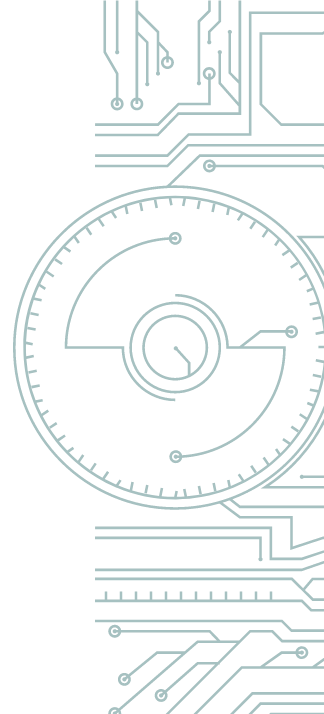
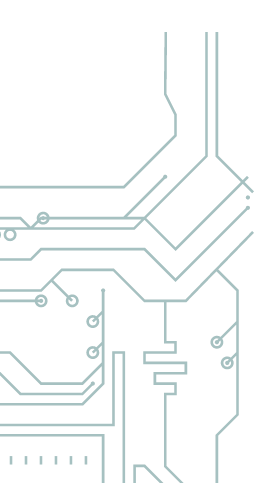
TASKS FOR THE SUPERCOMPUTER
Due to the nature of the physical processes involved, the calculations must be carried out on a very dense ‘numerical grid’, the minimum number of elements being 70 million. The calculations in this case must be carried out in parallel on many nodes. An additional complication is the analysis of transient processes, which significantly increases the time taken for the calculations and the size of the resulting files.
01.
During the project, comprehensive numerical simulations, validations of the proposed mathematical models and analyses of the results obtained were carried out qualitatively (visit of flows and temperature changes in the workspace) and quantitatively (analysis of thermal-fluid parameters together with analyses of mechanical and thermal power).
02.
The calculations were carried out in two different numerical environments: a commercial one, Ansys CFX and Fluent, and an open source one, OpenFOAM.
BENEFITS OF COOPERATION WITH WCSS
Significant reduction in calculation times.
The increase in the number of numerical elements, which has significantly influenced the quality of the calculations, particularly in the so-called hydraulic and thermal boundary layer.
The so-called time step was reduced, which significantly improved the quality of the results obtained.
Technical support in the process of installing and operating the software.
Flexibility for administrators regarding the technical capacity used.
Direct technical communication between the system administrator and the software developer.

6 m3
OPTIMISATION OF LARGE CAPACITY MIXERS

70 million
MINIMUM NUMBER OF ELEMENTS

300%
REDUCED MIXING AND HEATING TIME
EFFECTS
The development of methodology for carrying out numerical calculations for large-volume mixers. In the final stage of the calculations carried out, it became necessary to implement the properties of non-Newtonian fluids into the model. Equations such as the continuity equation, the momentum equation (Navier-Stokes) and the energy equation were proposed and implemented for the process.
A series of numerical calculations were carried out for existing mixers. The results of the numerical calculations had a high degree of convergence compared to the actual data. The mixers were then optimised in terms of mixing time in combination with the heating process.
Demonstration of the possibility of optimising the plant design using advanced numerical techniques such as CFD. In one of the cases analysed, it was possible to significantly reduce mixing and heating times by almost 300%.
Analyses and numerical algorithms are versatile enough to be applied in the lower scientific and industrial field related to the design and optimisation of mixers, e.g. paints, pharmaceuticals, building materials, food products.
Consultation of analyses with local product manufacturers in Lower Silesia – transfer of knowledge and analyses to operators.

6 m3
OPTYMALIZACJA MIESZALNIKÓW O DUŻYCH OBJĘTOŚCIACH

70 million
MINIMUM NUMBER OF ELEMENTS

300%
REDUCED MIXING AND HEATING TIME
EFFECTS
The development of methodology for carrying out numerical calculations for large-volume mixers. In the final stage of the calculations carried out, it became necessary to implement the properties of non-Newtonian fluids into the model. Equations such as the continuity equation, the momentum equation (Navier-Stokes) and the energy equation were proposed and implemented for the process.
A series of numerical calculations were carried out for existing mixers. The results of the numerical calculations had a high degree of convergence compared to the actual data. The mixers were then optimised in terms of mixing time in combination with the heating process.
Demonstration of the possibility of optimising the plant design using advanced numerical techniques such as CFD. In one of the cases analysed, it was possible to significantly reduce mixing and heating times by almost 300%.
Analyses and numerical algorithms are versatile enough to be applied in the lower scientific and industrial field related to the design and optimisation of mixers, e.g. paints, pharmaceuticals, building materials, food products.
Consultation of analyses with local product manufacturers in Lower Silesia – transfer of knowledge and analyses to operators.
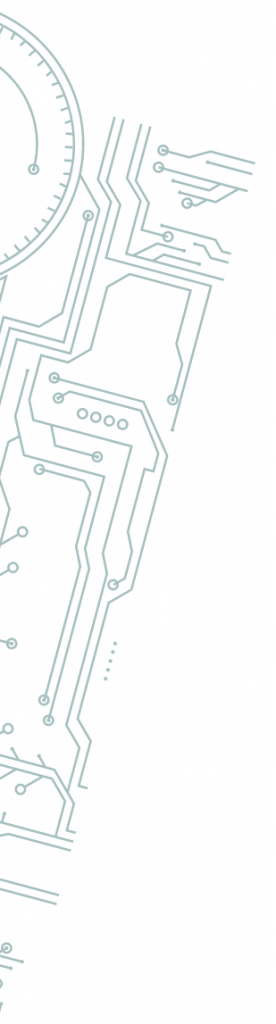
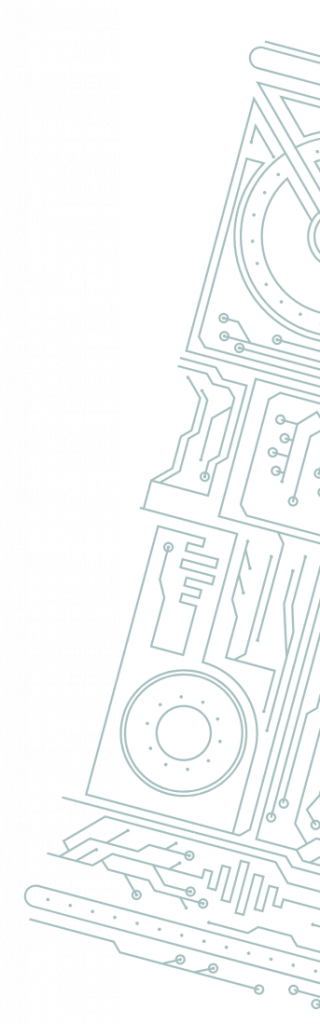
RECOMMENDATION
RECOMMENDATION
“Professional service for high-powered computing servers – software installation and configuration went smoothly, also the queuing system works flawlessly.
Access to a unique computing infrastructure.
Quick response to problems that arise during work.
Technical support in the process of installing and operating the software.
Flexibility in access to computing nodes.
Professional technical assistance at every stage of project execution”.
Ph.D. associate professor SŁAWOMIR PIETROWICZ Eng, WUST PROF.,
PH.D. PRZEMYSŁAW BŁASIAK Eng., PH.D. JÓZEF RAK Eng.
DEPARTMENT OF THERMODYNAMICS AND RENEWABLE ENERGY SOURCES,
WROCŁAW UNIVERSITY OF SCIENCE AND TECHNOLOGY